As some of you may know
Billy was apprenticed in Glasgow and there learned to make furniture and
engrave glass and with those skills he came to Canada some 25 years ago
and now runs his shop and internet business from Kimberley. In fact
it is by chance that I got here just in time as in two weeks time he will
be closing the retail shop to concentrate on wholesale and internet sales
and so this will turn out to be a wee historical archive :-)
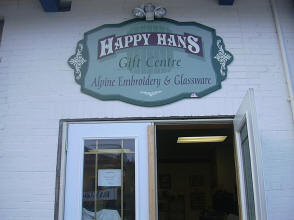
This is the outside of the shop with Billy and
Debbie at the door
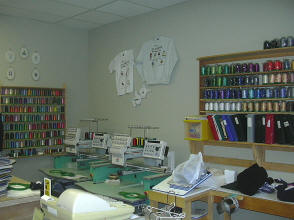
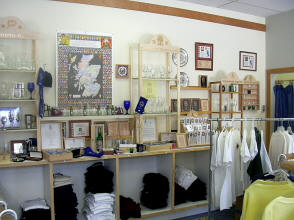
And so you can see the inside of the shop
where all kinds of products are for sale and all can have clan crests,
logos and anything you want engraved or woven onto them
Clan T-Shirts are very
popular so I thought I'd follow Debbie around to see how she does it
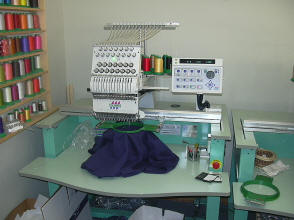
Here you can see Debbie setting up the sewing
machine
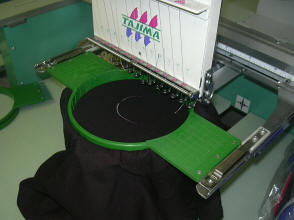
On the wall you can see all the various
threads you can use and on the right we start making a Clan Wallace
T-Shirt
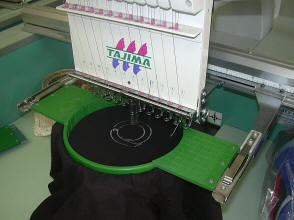
On the left picture you can see the stitch
count on the LCD display and also the progress being made with the crest
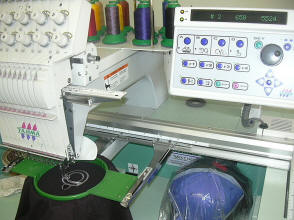
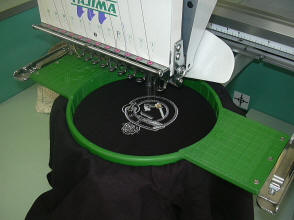
Getting there.. we are now at 7000 stitch
count
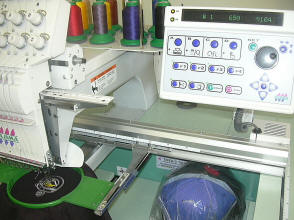
We've now gone over 9,000
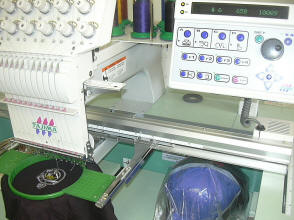
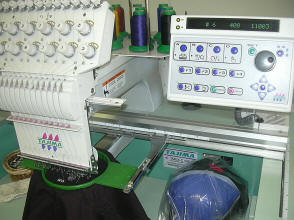
An error code on the LCD screen shows a thread
has broken so Debbie needs to re-thread that and then off we go again over
the 11,000 mark
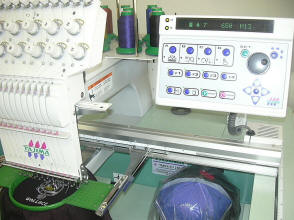
And the sewing is now complete
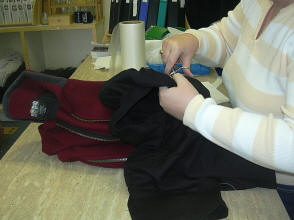
But of course there is always a wee thread
sticking out somewhere so the job is finished by hand. Debbie also told me
that there is a very slight mark on the T-Shirt where it is held in the
holder so this is also removed by hand during this final process.
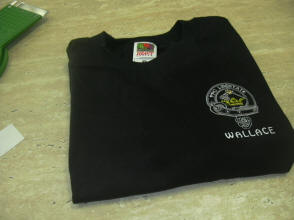
And the finished product ready to go into a
bag and be shipped of to the customer
Of course what you don't
see are the hours of work to create the authentic graphics and digitize
them into the computer to make all this happen. I'm told depending on how
complex the design is it can take from between 11,000 to 26,000 stiches to
complete a design.
The next project I wanted
to follow was the decanter and four whisky glass boxed set. I was
most impressed with the sheer amount of work needed to complete this and
the attention to detail that goes into it. I can well understand why
some companies take a number of short cuts but due to the standards set by
Billy he simply doesn't allow anything but the highest standards and I'll
show you what I mean as we work through this process.
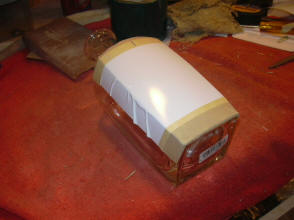
Billy first needs to set everything up on the
computer to interface with the laser that will cut the glass and put on
the shield. As you can see he needs to protect other parts of the glass so
a special covering has to be applied before the laser work starts.
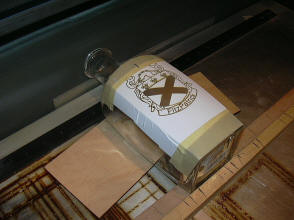
The depth of cut is also important and here
you can see work in progress and then the complete design at the end of
the laser process
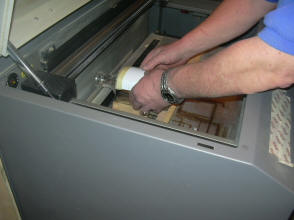
You can see how it is critical that the
decanter is positioned perfectly for the cutting process and this took
some time to set up correctly
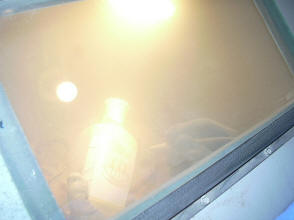
Now this totally surprised me as I thought
with the laser cutting complete that was it but far from it. Billy
actually sands the cut to produce a smooth finish. You can see he needs to
wear special protective gloves for this and you can likely just make out
the decanter being sanded in the picture on the right. Billy tells
me that most engraved glass is in fact just laser cut and if you run a
finger over the engraving you will feel a slight roughness. This
sanding process makes it totally smooth.
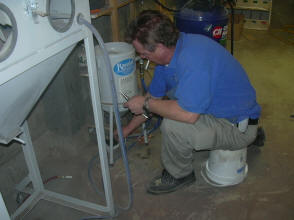
Of course you do need to adjust the pressure
so that the job is done correctly. Billy showed me how easy it was to cut
a hole in the glass with this sander and it didn't take long at all so you
do need a special kind of skill to do this correctly.
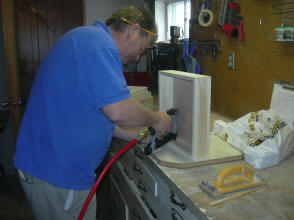
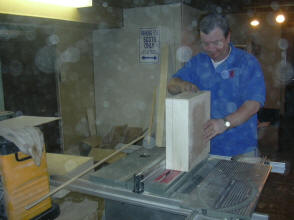
And to my astonishment Billy also makes his
own boxes!
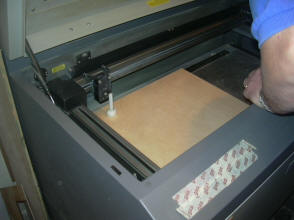
Debbie gets on with removing the masking tape
from the glasses and decanter and getting them sparkling while Billy gets
on with the presentation box. Here he is ensuring the box is at the
correct hight to get the perfect cut.

You can see the laser cutting in progress here
but again there is another surprise. To get the right depth of cut for the
box Billy does this in two passes. He found that when cut to the correct
depth with one pass of the laser you got a very slight scorching on the
wood. Due to this he decided to do a first cut to half the depth and
then repeat again to get the final cut. On the upper right you can see the
complete first cut and below the final second cut.
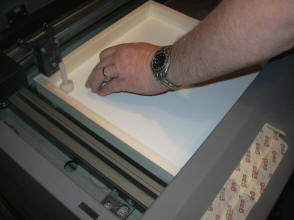
Billy now sets things up to engrave the
history of the family onto the inner lid and again it is essential the
right hight is set to get the best result.
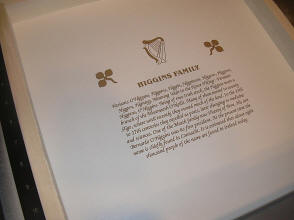
By being engraved into the wood it should
last for generations unlike other products where they simply put it on
paper and stick it onto the lid. Just another aspect of those
special touches that make Billy's products ones to be handed down to
future generations.
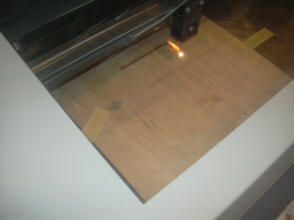
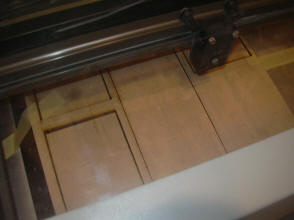
The above three pictures show how the insert
for the box is done and of course will hold the glasses and decanter
firmly in the box.
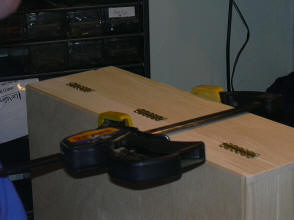
Again another special touch. Billy uses
3 hinges where others use just two and even more impressive, 8 wee nails
are used to secure each hinge whereas many would use four. It's these
little details which make the finished product really special.
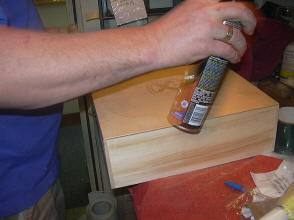
And a final wood polish to complete the job
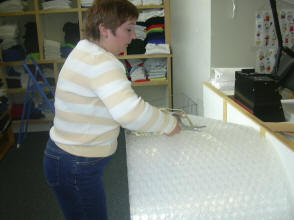


And as you can see the work was not yet
complete as the product needed to be dressed and you can see the steps
above taking you through to the complete presentation.
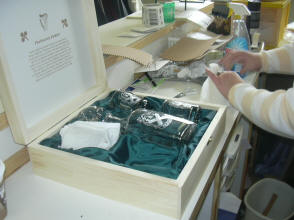
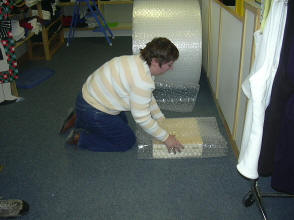
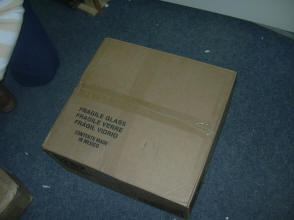
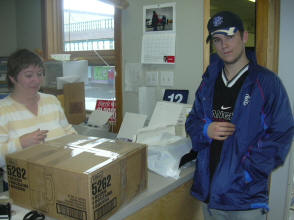
And as you can see this presentation set was
heading for New Zealand so it had to be packed well to ensure it arrived
in tiptop condition. It was then down to doing the paperwork for shipment
and son Donald was acting as postman and was taking it down to the post
office for shipment.
So by the time you've gone
through all those steps I'm sure you'll be as amazed as I was in seeing
just how many processes you had to go through and all these extra wee
details that Billy puts into the finished product. It truly is a family
business and of very high quality.
Should you be interested in
purchasing one of those decanter sets or a T-Shirt you can visit his web
site at
http://www.familycrests.ca
And just to show what else
you can get up to how about this for a T-Shirt!
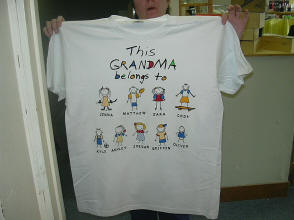
I'm getting a new logo
designed and hope to have it next week. Once it arrives I'm going to
be discussing with Debbie and Billy as to the range of merchandise I'll
put it on and what to offer. I'll include a special page on this as
you'll be able to see why certain merchandise was selected and also we'll
go through the digitising process of the logo so it can be used on various
merchandise. |